The
SCHWARZE-ROBITEC
service starts before the installation of your machine with
advice on how to reach your goals. With our know-how and
more than 80 years experience, we have the best solution
competence in the industry. Our customer service provides
comprehensive service for the life of our machines, whether
spare parts supply, on-site maintenance or the updating of
your machines.
SCHWARZE-ROBITEC also trains your
staff to work with our machines in our modern training room.
INSPECTIONS To ensure availability of your machines, we
recommend a regular inspection of the machine by the
service personnel of
SCHWARZE-ROBITEC.
REPAIRS Even
if the machines of
SCHWARZE-ROBITEC have the highest
durability and the longest economic lifetime, it is
possible that there is a need for repair after an
inspection or a failure.
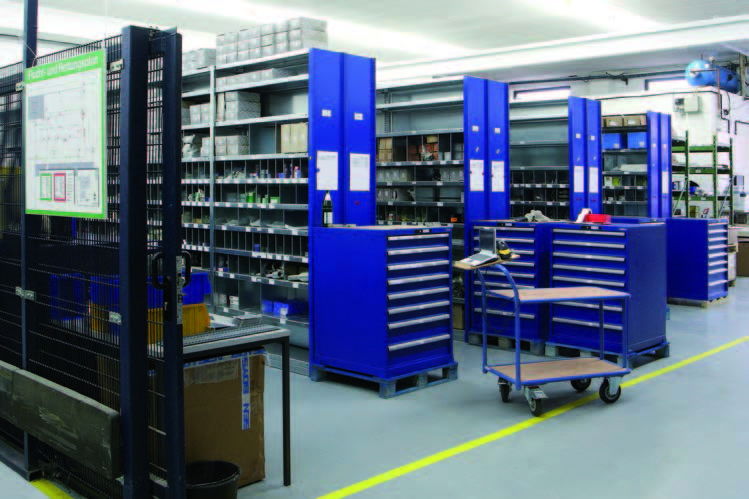
UPDATES The
update potential of a machine results partly from the
development of new techniques and components, especially
in control engineering, but also from new conditions
such as a change in engine integration in the
manufacturing process.
|
|
MAINTENANCE SCHWARZE-ROBITEC
handles the maintenance of your tube bending machine
with world-class attention: the lowest
possible downtime of each machine is important. Through
factory
trained personnel, the lifetime of the machine can be
extended, the machine up-time can be increased and
the use of the machine and the operating procedure can
be optimized. Our staff has decades of experience in
tube bending technology. Whether spare parts, advice and training for your
maintenance team, or complete maintenance by
SCHWARZE-ROBITEC
, we can react flexibly to your requirements.

SPARE-PARTS SUPPLY
SCHWARZE-ROBITEC
offers a high availability of spare parts over the
whole lifetime of our machines. Some of our machines
have been in service for over 30 years in a three-shift
operation. |
|
|